The world of manufacturing and metallurgy relies heavily on electric melting furnaces, and with good reason. These furnaces are essential in the production of metals like steel, iron, copper, aluminum, and alloys. Industrialists can rely on electric melting furnaces for their high melting efficiency, good electricity saving effect, good metal component uniformity, less burning loss, speedy temperature rise, and easy control of temperature. In this blog post, we shall delve into the specifics of melting furnaces for steel, medium frequency induction furnace, electric melting furnace, and other essential aspects of metal melting equipment.
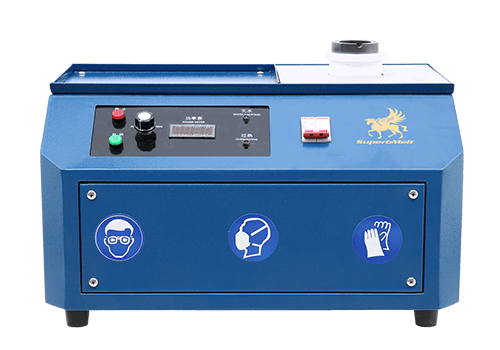
Melting Furnace for Steel
Steel manufacturers worldwide rely on electric melting furnaces for their melting needs. These furnaces offer a tremendous advantage in terms of energy efficiency compared to coal or gas furnace systems. Moreover, electric melting furnaces can equip automatic SCADA systems that offer temperature level monitoring, and automatic strategies can help optimize them to improve melting performance.
The steel-making procedure entails transferring material from raw iron ore to a high-grade metal. Steel melting allows manufacturers to create a uniform product that has standardized physical and chemical properties.
Steel melting furnaces employ advanced technologies like medium frequency induction furnaces and electric melting furnaces to provide steel melting services. While electric melting furnaces offer a better melting experience, medium frequency induction furnaces are the most popular furnace for melting steel. These furnaces melt the steel by inducing an electromagnetic field to produce heat in the metal's core.
Medium Frequency Induction Furnace
Medium frequency induction furnaces are perfect for melting, iron, steel, or any other metal. They work by using a magnetic field to generate electrical eddy currents within the metal. The induced electrical currents create resistance, which converts to heat in the metal, producing temperatures in the range of up to 2400°C. The furnace uses electromagnetic induction to fuse metal materials.
If you're looking for a furnace that uses less energy, improves the quality of your melting experience, and withstands high temperatures, the medium frequency induction furnace is the best choice for you. This furnace is an essential tool for steel melting, copper melting, and aluminum melting, among other metallurgical melting processes.
Electric Melting Furnace
Electric melting furnaces are highly efficient and come fitted with advanced technology to enhance the melting processes of different metals. These furnaces use electricity to create heat, enabling them to achieve higher melting temperatures than traditional coal or gas-fired furnaces.
Electric melting furnaces have the advantage of uniform heating with minimal temperature fluctuation. The precise temperature control it offers makes it even more attractive to manufacturers. The heat generation process ensures minimal emissions and reduces the carbon footprint associated with traditional furnaces.
The furnace unit is highly customizable, and the heating coils can be tailored according to the specific needs of the melting process. The electric melting process is well-supported by automation and the Internet of Things (IoT), which enables manufacturers to remotely monitor their melting processes and access data like temperature levels.
Metal Melting Equipment
Metal melting equipment comes in different forms, including furnaces, casting machines, and melting pots. Crucible melting, in which an open melting pot is used, is the most common method for melting bulk metals.
Most furnaces employ electromagnetic induction, electric arc, or gas heating methods to generate heat to melt metal. These furnaces include induction furnaces, arc furnaces, and resistance furnace.
Energy Saving Furnace
Industrialists prefer energy-saving furnaces for obvious reasons. These furnaces use high-quality insulation and cooling systems to ensure there is minimal energy loss, which leads to a significant reduction in energy consumption.
Energy-saving furnaces like medium frequency induction furnaces utilize modern technologies that consume less power to achieve the desired temperatures, thus reducing production costs.
Temperature Control Furnace
Precision temperature control ensures that furnaces can maintain a steady temperature throughout the melting process. This is crucial for consistency in the final product. Furnaces employ temperature sensors placed at various points on the furnace to monitor the temperature closely. A dynamic feedback mechanism integrated into the furnace ensures that the desired temperature is maintained throughout the melting process.
In conclusion, the world of industrial metals relies heavily on electric melting furnaces. Medium frequency induction furnaces, electric melting furnaces, and other machines are essential melting processes employed by steel, copper, aluminum, and alloy manufacturers worldwide. The advantages of these furnaces include high melting efficiency, good electricity saving, uniform metal component, less burning loss, speedy temperature rise, and easy control of temperature.