Product Name | Thin plate rolling mill | Related subjects | Machinery,Industrial production |
Category | Machinery | Subject | Metallurgical engineering |
Brand | Runxiang | Place of origin | Guangxi, China |
Related fields | Rolling mill process | Whether custom | Yes |
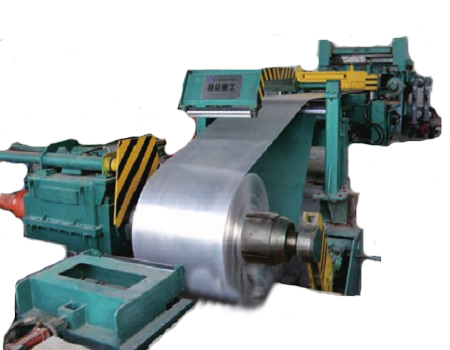